Types, applications, technical requirements and development suggestions of new materials for aviation engineering in my country
With the development of technology, traditional metal materials are being replaced by composite materials, and the amount of composite materials has become an important symbol of a new generation of civil aircraft. In the future, with the technological progress and scale expansion of the domestic large aircraft industry, the demand for composite materials processing products and services from the aerospace industry will show a growth rate higher than the global average. Future development will bring a strong composite material market Demand motivation.
This article will focus on the main application technology requirements and development status of new materials in my country’s aerospace industry, introduce research hotspots and cutting-edge technologies such as lattices, nanocomposites, multifunctional materials and structures, and discuss their applications and development trends. Provide reference for the application of new materials in aeronautical engineering.
1. The dominant position of metal materials
High-temperature alloys, titanium alloys, high-strength steels and aluminum alloys account for more than 95% of technical materials in the aerospace industry and commerce, and the mass percentage of metal structural materials will take the first place in various aircraft and engines for a long time. It is estimated that in the next 10 years or so, the demand for super alloys, titanium alloys, and high-strength steels will still account for a large proportion.
At present, titanium alloy is the main material for compressors, accounting for about 25% of the mass of large commercial engines. For example: RB-211-535E4 high-pressure electronic compressor uses MI829 titanium alloy produced by a British company; several major aircraft and engine manufacturers in the United States are considering using Ti-15V-3Al-3Cr-3Sn titanium alloy as a composite in aircraft and engines. Metal matrix.
2. Advantages and main types of composite materials
1. Advantages of composite materials
(1) Optional
In the use of composite materials, according to the expected use environment of different components and different conditions and requirements, the materials used for various components can be selected reasonably to meet the expected use purposes of the components, and ensure the mechanical, thermal, acoustic, optical, electrical, Good anti-corrosion and anti-aging properties, so as to meet the actual use performance of large-scale engineering building structure design.
(2) Material and structure integration
The connecting structure between composite connecting parts and various types of materials is a structure that is processed and formed at the same time, and composite parts are generally not processed separately. This processing technology makes the connection structure of various materials good in integrity, reduces the number of various material connection parts and various material structure connectors, shortens the cycle of various material connection processing and forming operations, and reduces material production costs. Improve the reliability of the material production line.
(3) Compound effect
The properties of composite materials are formed by the combination of various materials through different processes. It is not a simple mixture of several different materials, but new physical properties formed according to a composite process effect, which other composite materials do not have. New composite process effect performance. Using composite process effects, composite materials can effectively overcome the physical performance defects of other single materials.
2. The main types of composite materials
The main types of new composite metal materials used in aerospace include resin-based metal composite materials, metal resin-based molten composite materials, and carbon oxide/silicon-based carbon metal composite materials. Various resin-based metal composite materials are used in modern aviation industry technology. The application is wide.
(1) Advanced resin-based composite materials
Composite resin-based new composite reinforced materials are based on various high-performance composite resins as the main matrix, with various high-performance continuous composite fibers as the main materials, and are made of reinforced composite materials through certain new composite material process transformations. It is a composite The performance is obviously better than that of the new materials of the original composite components. Compared with the current traditional alloy materials in the main structure of stainless steel and other aluminum alloys, the density of the new alloy material is about 1/5 of that of ordinary steel and 1/2 of that of ordinary aluminum alloy, and its specific strength and specific modulus are far Higher than steel.
(2) Metal matrix composite materials
The main types of composite metal matrix composite materials widely used in the aerospace industry refer to metal composite materials based on light-strength metals such as alumina, magnesium, and titanium, and other high-strength second-phase alloys as the basic reinforcement. This composite product has good electrical conductivity, thermal conductivity, pressure and high temperature resistance, lateral movement performance, low material consumption and excellent material sustainable processing. The metal matrix composite parts are shown in Figure 1.
Third, the application of composite materials
1. Application on large aircraft
The Airbus A380 is a four-axle, twin-engine, 550-seat ultra-large long-range branch wide-body light passenger aircraft developed and produced by the European Airbus Industry Company. Among them: 25% of the main components of the civil aircraft body are made of color reflective composite material manufacturing process design, and 22% are made of color reflective carbon fiber reinforced plastic (CFRP).
2. Application on military aircraft
The application of advanced aircraft composite structural materials in military aircraft has a history of more than 30 years. From the beginning, non-load-bearing structural components have gradually developed and expanded to include vertical tails, horizontal wings, stabilizer wing surfaces, rudders, ailerons, and front and rear fuselages. The secondary and main non-load-bearing structural components such as the skins on the front and rear wings. For example, the European A400M aircraft is a new type of first-generation large military air transport aircraft, and its composite material technology and application have made new technological leaps.
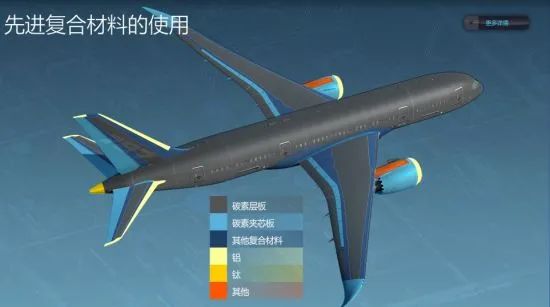
4. New composite material technology
With the continuous development of new manned aerospace vehicles, new composite materials have increasingly higher requirements for high efficiency, low cost, long service life, high reliability, and overall comprehensive performance of materials and component structures. In order to fully meet the needs of this composite application, various new new composite materials have emerged, but the performance of these new composite materials is not comprehensive. Therefore, it is necessary to continue to explore new types on the basis of improving the application performance of existing composite materials. The application potential of composite materials. Ultra-light composite materials and new structural composite technologies can be used to continuously increase the comprehensive performance of composite materials to meet the needs of versatility.
1. Ultra-light materials and structures
(1) Advanced grid reinforcement structure
This structure has attracted much attention because of its high degree of automatic visualization design and superior potential applicability. In the 1990s, a paper by Stanford University gave an isotropic layer mesh fiber reinforcement structure with a mesh fiber material reinforcement layer and CFRP as a fiber reinforcement layer, which improved the ratio of the mesh structure. The stress intensity and structural specific modulus enhance the corrosion resistance of the grid structure, and the use of this automated structure manufacturing process method can greatly reduce the manufacturing cost.
(2) Lattice composite material
More than 10 people, including Professor Evans of Harvard University, Professor Ashby of Cambridge University, and Professor Gibson of Massachusetts Institute of Technology, took the lead in successfully proposing the concept of lattice composite materials with a crystal lattice structure (molecular structure) in three-dimensional space. The high specific strength, high specific rigidity and versatility of this type of composite materials have attracted more and more attention from my country's materials science. In recent years, light composite metal fiber foam composite materials and lattice composite sandwich panels with new honeycomb structures have been widely used in manned aviation and space aerospace main structures, especially large-scale aviation main structures. The structure of the lattice core material is shown in Figure 2.
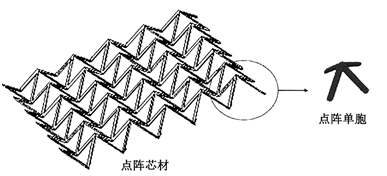
(3) Nano-fiber composite materials
Due to its unique chemical properties, nano-system materials have great scientific research value in practical applications and scientific theories, and have broad application development prospects. In recent years, it has gradually become an important research and development direction in the field of materials science and technology in my country, and is hailed as a promising chemical material in the 21st century.
2. The connection method of composite materials
In aerospace and chemical industries, many different materials are used in the same equipment. Realizing the connection between different materials, especially the materials that are difficult to be welded, is a problem that must be solved in the overall design of the equipment. At present, the more commonly used connection methods include riveting, screwing and conventional welding.
5. Suggestions for the development of new materials for my country's aviation engineering
China's new composite metal materials are new materials that have been gradually developed to meet the actual national defense and civil aerospace market needs. Affected by the functional division of material systems in various application fields and the independent innovation and development of enterprises, new materials still have many types of raw materials and process grades, uneven maturity of materials, low material performance or duplication with similar high-level materials, and low cost performance And other outstanding problems, and the import supply chain of raw materials cannot meet the domestic market demand. In addition, the product performance, quality, specifications, price, and after-sales supply service capabilities of domestic aerospace composite materials are far from fully satisfying the actual needs of the national defense, aerospace and civil industries. Especially after China’s entry into the WTO, it has faced severe challenges in terms of protecting independent R&D intellectual property rights, innovation, and continuous improvement of market competitiveness.
At present, my country is vigorously developing aviation equipment such as regional military aircraft, regional civil aircraft, and large commercial regional passenger aircraft. The continuous development of these application fields urgently requires good composite materials. Although after years of research and development, my country's aviation composite materials have gradually developed into a technical system that has basically met the relevant technical standards for aerospace application models, but there is still a certain technological gap with developed countries. Therefore, it is necessary to conduct key basic research and technological innovation in some key technical fields of metal composite structural materials, so as to establish the necessary material guarantee for the development of the national defense and aerospace industries.
6. Conclusion
New materials are an important material basis for aeronautical engineering and other related fields, which can improve the performance of various aspects of aeronautical equipment and parts, so that the equipment can meet the needs of use. In the future development, it is necessary to continuously research related materials and accelerate the integration of technology, equipment and technology to promote the development of aerospace industry.